Seafunks
Themenersteller
Download der Dateien und gesamten Dokumentation: Dropbox

1. Vorwort
Die Idee einen Filterhalter selber zu konstruieren kam mir, nachdem ich die Preise für kommerzielle Filterhalter für das 150mm-System sah. Bei Startpreisen von 120€ (ohne entsprechenden Adapter) fiel mir nach dem Kauf des ohnehin nicht ganz günstigen Sigma 20mm/1.4 Art die Kinnlade herunter.
Lange hat es gedauert, nun ist er endlich fertig: Mein eigen konstruierter Filterhalter für 150mm Plattenfilter.
Was den Filterhalter ausmacht:
2. Der Druck
Da das ganze Projekt auf dem 3D-Druck (bzw. FLM = Fused Layer Modeling) basiert, ist ein solcher natürlich nötig, um überhaupt beginnen zu können. Ich werde hier nicht zu sehr ins Detail gehen, da ich davon ausgehe, dass diejenigen, welche einen 3D-Drucker besitzen sich damit auch auskennen.
Ich habe den Halter auf dem Ultimaker 3 gedruckt. Dieser hat den Vorteil, dass er mit zwei Extrudern zwei Filamente drucken kann, unter anderem auch wasserlösliches PVA, welches sich hervorragend für die Stützstruktur eignet. So kann man das Modell nachher einfach in Wasser einlegen und mit etwas Geduld und schrubben löst sich die Stützstruktur einfach auf. In dem anderen Extruder ist dann das Material für das Modell, idealerweise schwarzes PLA. Der benötigte Bauraum beträgt mindestens 170 x 170 x 31mm.
Die Dateien für den Druck liegen als .stl vor. Dieses Format wird von den meisten Slicern erkannt. Wer zufälligerweise auch einen Ultimaker 3 benutzt, für den habe ich die Arbeit des Slicens bereits übernommen und die entsprechende .gcode-Datei angehängt. Der Druck dauert bei meinen Einstellungen etwa 62 Stunden.
Insgesamt werden benötigt:
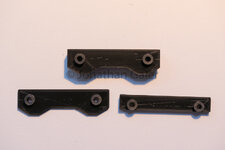
Alle Teile bis auf die Formatteile und das Frontteil lassen sich ohne Stützstruktur auf fast jedem herkömmlichen 3D-Drucker drucken.
Zusätzlich sollte erwähnt werden, dass PLA nicht gerade sehr temperaturbeständig ist. Zwar liegt der Schmelzpunkt bei ca. 200°C, sehr heißes (ca 50°C) Wasser reicht jedoch auch schon aus, damit sich das Teil im Nachhinein verzieht. Je höher die Temperatur, desto leichter löst sich das PVA, dennoch würde ich hier eher geduldig vorgehen, insgesamt sind zwei Drucke und damit zwei ganze Wochenenden Druckzeit der Temperatur zum Opfer gefallen. Eine hohe Lufttemperatur (bspw. im Auto mitten in der prallen Sonne) um die 50°C hat dem Halter zumindest im Fotorucksack bisher nichts anhaben können.

Um zu veranschaulichen, warum ein Drucker mit Dualextrusion nötig ist, anbei ein Bild einer Ecke der Front von einem Druck mit nur einem Material. Trotz Nachbearbeitung lässt sich nicht die komplette Stützstruktur entfernen. Zusätzlich gibt es einige waagerechte Überhänge, welche abgestützt werden müssen und bei Singleextrusion nicht die nötige Oberflächenqualität erfüllen. Gerne lasse ich mich vom Gegenteil überzeugen!

Hier mal ein paar Eckdaten, mit welchen Einstellungen ich gedruckt habe und zufriedenstellende Ergebnisse erzielt habe:

1. Vorwort
Die Idee einen Filterhalter selber zu konstruieren kam mir, nachdem ich die Preise für kommerzielle Filterhalter für das 150mm-System sah. Bei Startpreisen von 120€ (ohne entsprechenden Adapter) fiel mir nach dem Kauf des ohnehin nicht ganz günstigen Sigma 20mm/1.4 Art die Kinnlade herunter.
„Das muss doch auch günstiger gehen!“
– und wozu studiere ich überhaupt Maschinenbau, wenn ich nicht in der Lage sein sollte, eine eigene Version zu konstruieren? Und nachdem ich gesehen habe, was die Jungs von Logodeckel im 3D-Druck entwickelt hatten war klar: Darauf wird auch mein Filterhalter basieren. Gewisse Parallelen lassen sich sicher nicht abstreiten, dennoch gefielen mir ein paar Dinge nicht: Beispielsweise, dass man für jedes Objektiv einen eigenen Halter benötigt störte mich extrem. Ich möchte im Zweifelsfall nicht 3 verschiedene Systeme für 3 verschiedene Objektive mitschleppen. Zum anderen störte mich, dass man bei starken Graufiltern nicht mehr in der Lage ist, zu komponieren und zu fokussieren, sobald der Filter aufgesetzt ist. Daher sollte es schnell gehen, den Halter samt Filter zu entfernen. Lange hat es gedauert, nun ist er endlich fertig: Mein eigen konstruierter Filterhalter für 150mm Plattenfilter.
Was den Filterhalter ausmacht:
- Hält bis zu 3 Plattenfilter mit 150mm Kantenlänge (nur bis 2 getestet). Bei Benutzung von Verlaufsfiltern kann der untere Halter entfernt werden, die Filter halten trotzdem!
- Durch ein Bajonett können mehrere Formatteile für verschiedene Objektive montiert werden
- Mit nur einem kleinen Dreh lässt sich die Front samt Filter entfernen um zu fokussieren/komponieren
- Durch ein Bajonett können mehrere Formatteile für verschiedene Objektive montiert werden
- Mit nur einem kleinen Dreh lässt sich die Front samt Filter entfernen um zu fokussieren/komponieren
2. Der Druck
Da das ganze Projekt auf dem 3D-Druck (bzw. FLM = Fused Layer Modeling) basiert, ist ein solcher natürlich nötig, um überhaupt beginnen zu können. Ich werde hier nicht zu sehr ins Detail gehen, da ich davon ausgehe, dass diejenigen, welche einen 3D-Drucker besitzen sich damit auch auskennen.
Ich habe den Halter auf dem Ultimaker 3 gedruckt. Dieser hat den Vorteil, dass er mit zwei Extrudern zwei Filamente drucken kann, unter anderem auch wasserlösliches PVA, welches sich hervorragend für die Stützstruktur eignet. So kann man das Modell nachher einfach in Wasser einlegen und mit etwas Geduld und schrubben löst sich die Stützstruktur einfach auf. In dem anderen Extruder ist dann das Material für das Modell, idealerweise schwarzes PLA. Der benötigte Bauraum beträgt mindestens 170 x 170 x 31mm.
Die Dateien für den Druck liegen als .stl vor. Dieses Format wird von den meisten Slicern erkannt. Wer zufälligerweise auch einen Ultimaker 3 benutzt, für den habe ich die Arbeit des Slicens bereits übernommen und die entsprechende .gcode-Datei angehängt. Der Druck dauert bei meinen Einstellungen etwa 62 Stunden.
Insgesamt werden benötigt:
1x Frontteil (Filterhalter_Front.stl)
1x Formatteil (Filterhalter_Formatteil_<Format>.stl)
3x Halter Endhalter (Filterhalter_Halter_Endhalter.stl)
3x/6x/9x* Halter Abstandhalter (Filterhalter_Halter_Abstandhalter.stl)
0x/3x/6x* Halter Zwischenhalter (Filterhalter_Halter_Zwischenhalter.stl)
*Die zweiten bzw. dritten Mengenangaben beziehen sich auf die Möglichkeit 2 bzw. 3 Filter zu montieren.1x Formatteil (Filterhalter_Formatteil_<Format>.stl)
3x Halter Endhalter (Filterhalter_Halter_Endhalter.stl)
3x/6x/9x* Halter Abstandhalter (Filterhalter_Halter_Abstandhalter.stl)
0x/3x/6x* Halter Zwischenhalter (Filterhalter_Halter_Zwischenhalter.stl)
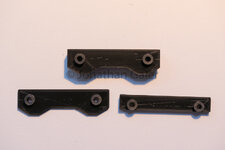
Alle Teile bis auf die Formatteile und das Frontteil lassen sich ohne Stützstruktur auf fast jedem herkömmlichen 3D-Drucker drucken.
Zusätzlich sollte erwähnt werden, dass PLA nicht gerade sehr temperaturbeständig ist. Zwar liegt der Schmelzpunkt bei ca. 200°C, sehr heißes (ca 50°C) Wasser reicht jedoch auch schon aus, damit sich das Teil im Nachhinein verzieht. Je höher die Temperatur, desto leichter löst sich das PVA, dennoch würde ich hier eher geduldig vorgehen, insgesamt sind zwei Drucke und damit zwei ganze Wochenenden Druckzeit der Temperatur zum Opfer gefallen. Eine hohe Lufttemperatur (bspw. im Auto mitten in der prallen Sonne) um die 50°C hat dem Halter zumindest im Fotorucksack bisher nichts anhaben können.

Um zu veranschaulichen, warum ein Drucker mit Dualextrusion nötig ist, anbei ein Bild einer Ecke der Front von einem Druck mit nur einem Material. Trotz Nachbearbeitung lässt sich nicht die komplette Stützstruktur entfernen. Zusätzlich gibt es einige waagerechte Überhänge, welche abgestützt werden müssen und bei Singleextrusion nicht die nötige Oberflächenqualität erfüllen. Gerne lasse ich mich vom Gegenteil überzeugen!

Hier mal ein paar Eckdaten, mit welchen Einstellungen ich gedruckt habe und zufriedenstellende Ergebnisse erzielt habe:
- Schichtdicke 0,1mm
- Wanddicke 0,8mm; Boden/Decke: 1mm
- Fülldichte: 100% Modell, 20% Stützstruktur
- Druckgeschwindigkeit: 70mm/s PLA, 35mm/s PVA
- Supportdeckendichte: 100%
Ich bin mit meinen Einstellungen sicher nicht an die Grenzen des Möglichen gegangen, Experimentieren und Posten der Ergebnisse gerne gewünscht!- Wanddicke 0,8mm; Boden/Decke: 1mm
- Fülldichte: 100% Modell, 20% Stützstruktur
- Druckgeschwindigkeit: 70mm/s PLA, 35mm/s PVA
- Supportdeckendichte: 100%
Zuletzt bearbeitet: